Process Flow
Lost Wax Casting
Lost wax casting is now called investment casting. It is a precision casting process with little or no cutting. It is not only suitable for precision casting of various types and alloys but also produces castings with higher dimensional accuracy and surface quality than other precision casting methods. We use two kinds of wax materials to produce steel castings, namely yellow low-temperature wax and green medium-temperature wax, to meet the needs of different customers.
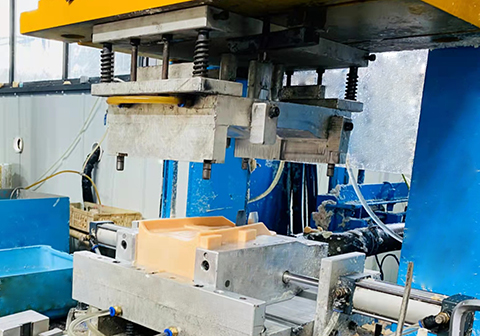
Creat Wax Patterns
The engineer completes the design and production of the mold according to the drawings. Use an automatic wax injection machine to make wax patterns. After the worker trims the wax patterns, it is handed over to the inspector for inspection. After passing the test, it will be transferred to the tree assembly process.
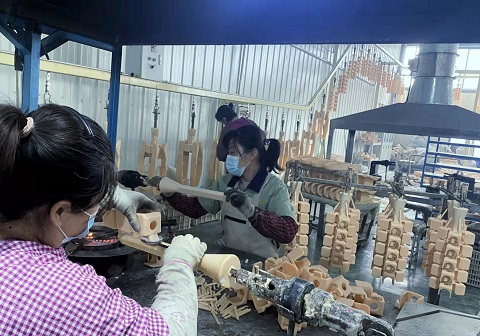
Tree Assembly
Wax patterns are connected to a central wax stick called a runner which includes the sprue, to form the tree assembly. It should be noted that different products have different tree forming processes to maximize benefits. The role of the central wax stick is to create a flow path for the alloy solution to flow into the various hollow crevices of the wax mold.

Shell Making
After the wax pattern tree is assembled, the robotic arms are used for dipping and sanding, and then the air-drying line is circulated and air-dried. As each layer is made, the shell is dry before proceeding to the next layer. Repeat this process until the wax tree is around the desired thickness and fully hardened.
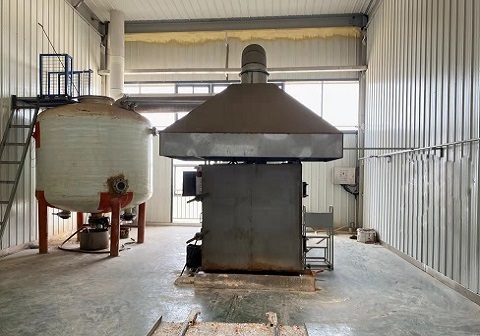
Steam Dewaxing
The shell will be dewaxed with a steam dewaxing kettle. The inverted shell can discharge wax and impurities better and more completely, which helps to improve the quality of the product surface and reduce defects such as porosity and shrinkage. At the same time, wax is also more convenient to recycle, efficient, and environmentally friendly.

Roasting & Pouring
Put the shell into the roasting kiln and roast it to the specified temperature and burn it through. The chemical composition of the molten steel is analyzed with a spectrometer to ensure that it is correct, and then the molten steel is poured into the shell. As the molten steel cools, the entire shell becomes a solid casting.
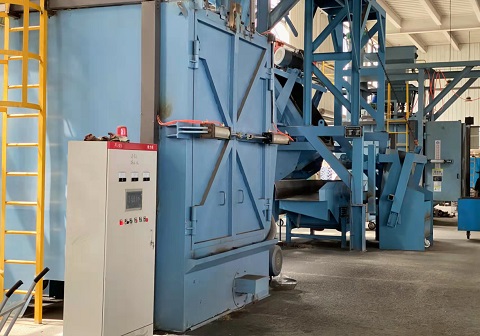
Post Treatment
After the molten steel cools and solidifies, the shell will be broken by vibration, and then will be cut, ground, shot blasted, inspected, heat-treated, etc. Some products will be required to mark the heat number for tracking. Normalizing, annealing, quenching, tempering, and solution treatment are the most commonly used heat treatment methods.
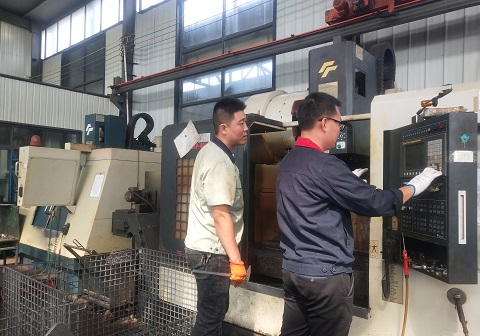
Machining
We provide not only steel castings but also CNC machining services, allowing us to provide our customers with a complete single-supplier solution from initial design to finished product. The machining workshop is equipped with several advanced CNC machining centers, CNC turning centers, CNC milling machines, CNC machining lathes, etc.

Final Inspection
Inspection is accompanied by all processes of casting, for this reason, our quality control laboratory is equipped with many inspections and testing equipment, such as CMM, spectrometer, metallographic microscope, tensile tester, impact testing machine, hardness tester, magnetic particle inspection machine, etc. to ensure dimensional accuracy and high-quality castings.
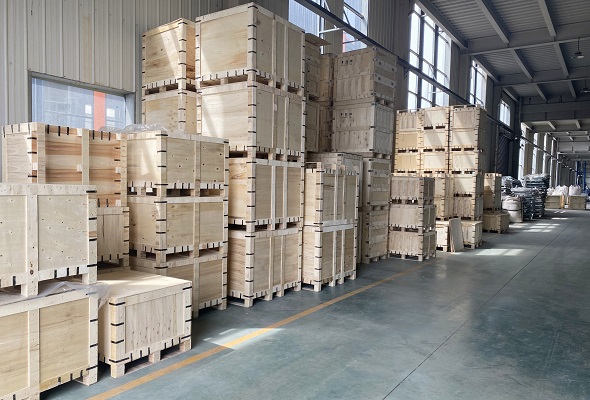
Packing & Shipping
Castings are rust-proofed with anti-rust water, then dried in a dryer and packed. Castings treated in this way have a clean appearance and remain rust-free for at least six months. The outer packaging is generally used in plywood cases, or according to customer requirements. Finally, it sends to the port for delivery to the customers. Qingdao Port is the nearest port to us.
Contact XJL Today
Upload The Drawings,Take a Break, You Will Get Your Free Sample
XJL is your premier resource for specialty investment precision castings.